Tin cans are a common container in our daily lives. We have seen its various product packaging. Tin can packaging is a form of packaging widely used in food, cosmetics, paints and other industries. Its printing The quality of packaging is directly related to product image and market competitiveness. This article will delve into the production process and printing methods of tin can packaging printing, so that readers can have a more comprehensive understanding of the technical characteristics and innovations in this field.
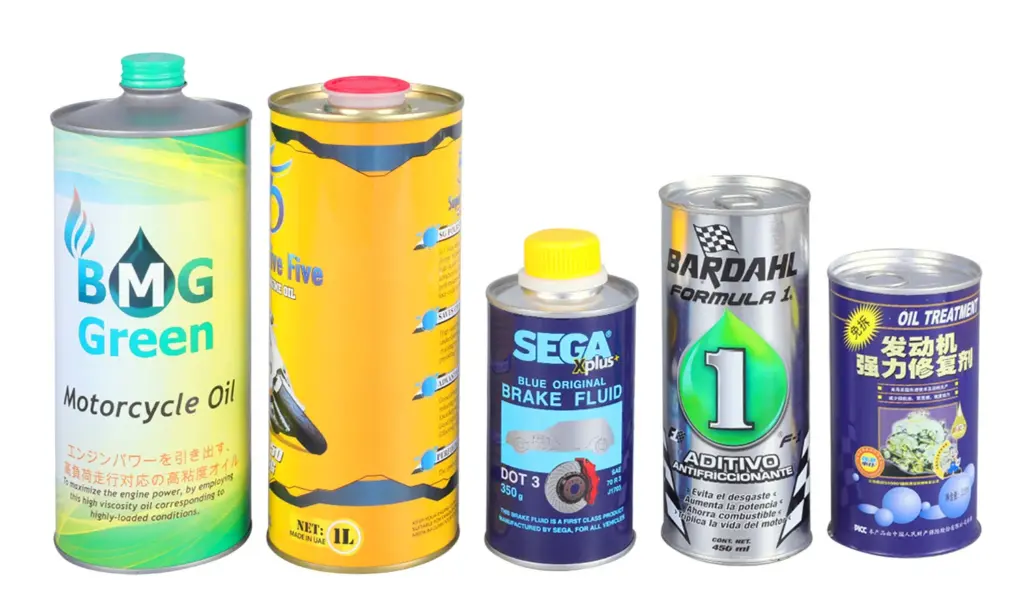
Tin can printing production process:
The production process of tin can packaging and printing is a complex process, including design, preparation, printing, processing and inspection. Tin can printing is a sophisticated and unique technique designed to provide products with high quality, durability and visual appeal.
Design stage
Before the production process of tin can printing can begin, a design first needs to be made. Designers use professional software to create artwork, taking into account product features, brand image and market needs. Tin can printing usually involves curved surfaces of metal materials, so designers must take these special constraints into account to ensure a perfect final effect.
Plate making preparation
Once the design is determined, the next step is preparation for pattern making. Platemaking is the conversion of the design into a printing plate that can be printed onto the surface of the tin can. This usually involves the creation of digital or photosensitive plates. The accuracy of this step directly affects the printing quality and details.
Printing process
Ink preparation: Before printing, you need to prepare ink suitable for the surface of the tin can. This may include metallic inks whose composition is specifically designed to adhere to metal surfaces and provide long-term durability.
Printer Setup: Tin can printing usually uses a rotary press, the settings of which need to be adjusted based on the design and tin can size. This ensures even ink transfer across the entire surface while maintaining print consistency.
Printing process: The tin can is placed on the printing press and the printing plate transfers ink to the surface of the tin can. Due to the curved surface of the tin can, printing machines are often equipped with special devices that adapt to the curved surface to ensure that the ink evenly covers the entire surface.
Curing and processing
After printing, the tin needs to go through a curing and processing stage. This includes:
Drying: The tin can is passed through the drying equipment to quickly dry the ink and improve the durability of the printing effect.
UV Curing: UV curing technology is sometimes used to ensure that the ink dries quickly and creates a solid surface.
Inspection and quality control
Finally, the finished product requires inspection and quality control. This includes checking print quality, color accuracy and overall appearance. Unqualified products will be excluded to ensure that the tin can printing delivered to customers is of high quality.
Excellent protection and quality assurance
Oil products need reliable packaging to ensure their quality and safety during transportation and storage. High-quality oil tank packaging and printing services not only focus on appearance, but also consider internal protection. Using innovative materials and printing technology, this printing service can provide oil products with excellent leak-proof, anti-oxidation and anti-pollution capabilities, ensuring that the products will not be damaged during transportation and storage.
Tin can printing process
This is the core link of the entire process. Tin can packaging often uses flexographic printing technology, which includes:
Flexible offset printing: Suitable for mass production, capable of printing multiple colors evenly and efficiently on the surface of iron cans.
Inkjet printing: For low-volume production or where personalized printing is required, inkjet technology offers the advantages of high resolution and fast changeover.
Detailed explanation of flexible offset printing:
Flexible offset printing is one of the commonly used methods in tin can packaging printing. Its production process includes the following steps:
- Plate preparation: First, the designer makes a printing plate based on the artwork, usually using a photosensitive plate or a digital plate.
- Pigment preparation: According to the characteristics of the iron can surface, suitable ink pigments are prepared to ensure full and stable color.
- Printing process: Using a flexographic printing machine, the printing plate transfers ink through a roller, and then the ink is transferred to the surface of the iron can. The high-speed rotating printing press can quickly complete the entire printing process while maintaining print quality.
- Drying and curing: After printing, drying and curing are required to ensure that the ink adheres to the surface of the iron can and forms a durable pattern.
Inkjet printing applications:
For small batches and personalized needs, inkjet printing technology provides flexible and efficient solutions.
- Digital design and output: Create artwork through computer design software, and then output it directly to the surface of the tin can, avoiding the traditional printing plate production process.
- High-resolution printing: Inkjet printers are capable of high-resolution graphics, showing finer details and colors.
- Fast switching: Inkjet printers have fast switching capabilities and can adapt to different design and printing needs in a short time.
In conclusion:
Tin can packaging printing is a comprehensive technology that involves multiple links such as design, preparation, printing and processing. Flexible offset printing and inkjet printing are common printing methods. Choose the appropriate technology based on production needs and design requirements. With the advancement of science and technology, tin can packaging and printing technology will continue to develop to meet the market’s continuous demand for personalized, high-quality packaging.
Pingback: Custom Tinplate Packaging - fanxuncan