What are the technical requirements for tinplate cans? What are the special requirements for printing ink? The following is a detailed introduction to you by Fanxun packaging container manufacturer.
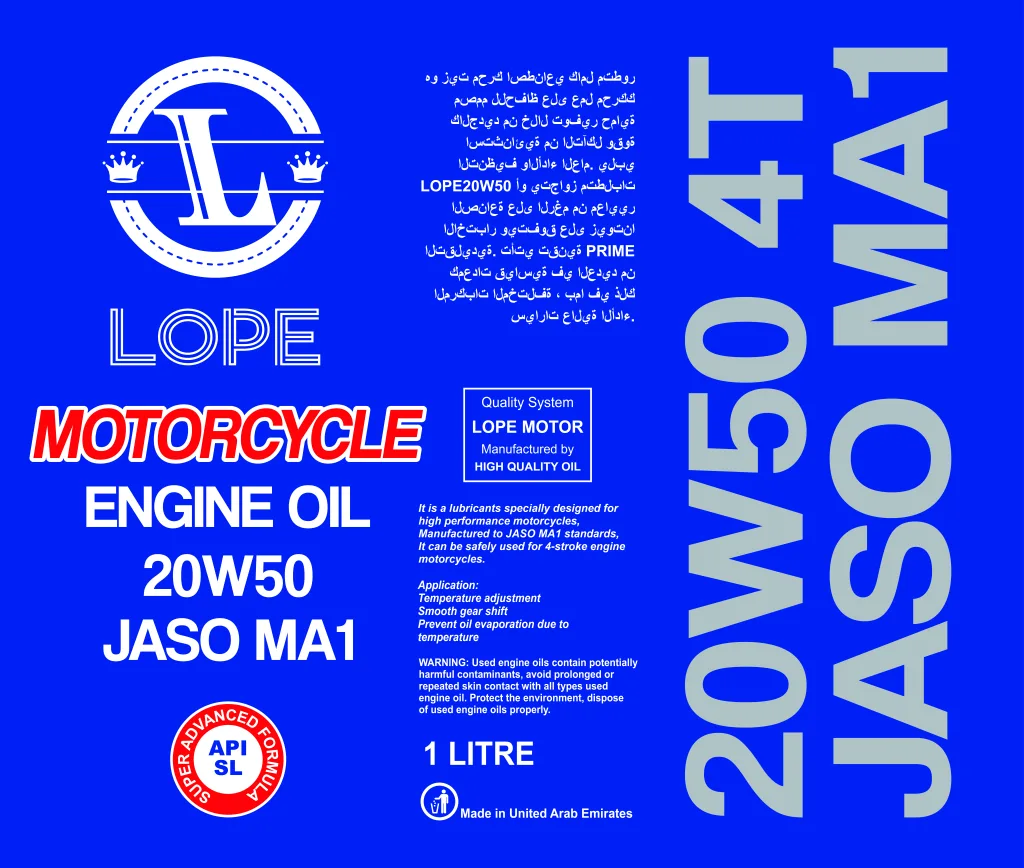
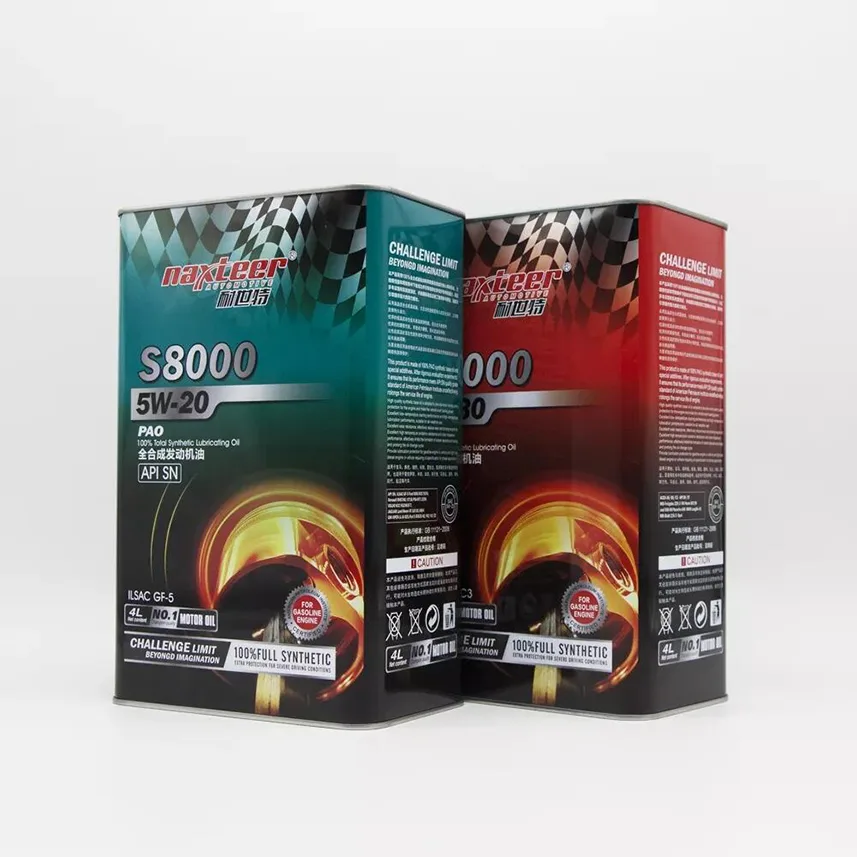
Tinplate can printing has special requirements for ink:
Printing inks are required to have good adhesion and mechanical properties
Because tinplate cans are mostly made into food cans, tea cans, biscuit cans, vesaire., and tinplate cans need to go through more than ten processes such as cutting, bending, stamping, and stretching, so printing inks are required to have a good effect on iron plate tinplate cans. adhesion and corresponding mechanical properties. In order to improve the ink adhesion, white ink needs to be printed on the tinplate can before printing. White ink is the basic tone of all printing patterns and has high brightness. Adding other high-energy inks increases the brightness of all colors, creating color gradations.
Requirements for printing white ink in tinplate can printing
The surface of the tinplate can is silvery white (or yellow) with metallic luster. It needs to be painted or printed white before printing color graphics and text. Due to the limited ink coating capacity, monochrome machines often have to go through two white printings. The whiteness can reach 85%. White color is an important standard for the printing quality of tinplate cans. It requires that the white ink has good binding force with the primer, does not turn yellow after being baked at high temperatures for many times, and is resistant to high temperature steaming without fading. Applying primer can improve the adhesion of tinplate cans and have good adhesion to white ink. The commonly used primer is epoxy amine-based, which is light in color, will not turn yellow after repeated baking, does not age, has good elasticity, and is impact resistant.
Requirements for color inks for tinplate can printing
In addition to certain water resistance, color inks printed on tinplate cans also have special requirements for them. Since the surface of the tinplate can has no water-penetrating solvent and needs to be dried, the ink should be thermosetting. There are high requirements for the coloring power and durability of pigments. In addition to the basic properties required for general offset printing inks, according to the characteristics of the printing iron, it should also have characteristics such as heat resistance, strong ink film adhesion, impact resistance, good hardness, cooking resistance and light resistance.
Drying process of tinplate can printing ink
In addition to certain water resistance, color inks printed on tinplate cans also have special requirements for them. Since the surface of the tinplate can has no water-penetrating solvent and needs to be dried, the ink should be thermosetting. There are high requirements for the coloring power and durability of pigments. In addition to the basic properties required for general offset printing inks, according to the characteristics of the printing iron, it should also have characteristics such as heat resistance, strong ink film adhesion, impact resistance, good hardness, cooking resistance and light resistance.
Drying process of tinplate can printing ink
In tinplate can printing production, the drying of ink is a complex physical and chemical reaction process. It is necessary to reasonably control the drying speed of ink and master the physical and chemical mechanisms of ink drying in order to effectively carry out fast printing operations and ensure product quality. Drying the ink too fast will reduce the normal transfer performance of the ink and affect normal production; it will cause the surface imprinting of the printing plate and the ink roller to weaken, the ink color will become lighter, the ink will dry out, and the ink transfer will be hindered; the dry layer of the printing plate will be outward. Expansion; Excessive desiccant will cause increased ink adsorption, making the blank parts dirty. However, if the ink dries too slowly, it will cause overprinting difficulties, blocking, sticking, vesaire. , the hardness is reduced; it is easy to cause scratches during the transmission process. Therefore, the drying speed of the ink should be appropriate, and it should not be too fast or too slow.
Special structure of tinplate can printing equipment
Because the substrate is tinplate, the auxiliary mechanism of the printing press is different from that of the paper offset printing press. Tinplate is insoluble in water and does not absorb solvents, so the ink on the tinplate can needs to be baked at high temperature to solidify the conjunctiva after the solvent evaporates. Therefore, a drying room is usually required during the printing process. The fully automatic printing line for tinplate cans is generally about 40-55 meters long and has sophisticated and large equipment. In addition, tinplate printing machines are controlled by single and double-piece magnets. The high hardness of tinplate materials also determines that advanced continuous iron feeding structures cannot be used during the printing process, which is different from offset printing machines in the structure of pushing, positioning and stacking parts.
Printing process of tinplate cans
Lithographic printing process of tinplate cans:
The biggest feature of lithography is that the printed pattern (ink-stained part) and the non-printed pattern are on the same plane. Lithographic printing is to print ink on a rubber roller, and then use a pressure roller to print on tinplate. Because the printing plate does not come into direct contact with tinplate ink and does not stain, it is suitable for high-quality printing, and even if the tinplate finish is not good, it will be overcome.
Hot stamping process of tinplate cans
After heating the tinplate, the post-processing process of embossing the pattern on the tinplate using tin foil is widely used because of its bright visual effect.
Letterpress printing process for tinplate cans:
Letterpress printing means that the graphic part on the layout is higher than the non-graphic part. The ink on the ink roller can only be transferred to the graphic part on the layout, while the non-graphic part does not require ink, thus completing the printing. A traditional printing technology that rolls ink on the tinplate can engraving plate and then embosses the tinplate sheet. The pressure printed on the tinplate can engraving plate can be adjusted as needed to create a deeper three-dimensional feeling.
Ink-free embossing process for tinplate cans:
It does not require heating, tin foil, or ink; it is a processing technology that is directly imprinted on the tinplate sheet, suitable for presenting the original texture of the tinplate or expressing it in a simple style.
UV printing process of tinplate cans:
Special ink is used to dry printing after being irradiated with ultraviolet rays. It is suitable for tinplate that is not easy to dry, or other flat materials, such as aluminum products, wooden boards, vesaire.
Screen printing process of tinplate cans:
Screen printing is a method of hollowing out the printed part on the printing plate and allowing the ink to transfer through the mesh. When the substrate is made of tinplate, aluminum plate, plastic and other materials, or has a curved surface such as a box or can, or has special printing requirements such as a floating surface effect, screen printing is mostly used.
Lithographic printing process of tinplate cans:
Flat printing is a relatively mature printing method at present. It is a fast and stable large-scale printing technology. It is suitable for mass printing of tinplate cans. It is a very good and economical choice when the printing volume is large.
Screen printing process of tinplate cans:
Screen printing is the traditional process of printing with a screen made of nylon thread. In metal printing, only a single color or a few colors can be used for registration printing. Because it is semi-manual production, if there are overlapping colors, it is not suitable for products with high precision requirements.
Silk screen printing process for tinplate cans
The surface of the tinplate can must be pre-treated after silk screen printing. The pre-treatment process of the surface of the tin can is also called pre-press processing. Pretreatment methods for the surface of iron cans include degreasing, polishing, drawing, oxidation, sand surface treatment, spray painting, vesaire. This method can be used alone or in combination to achieve the desired effect according to the different requirements of the product and the conditions of the underlying material.
The above is a brief introduction to the printing principles and processes of tinplate cans. I hope it can help you. You are also welcome to come and inquire!